Modular Solutions
Japan's Leading Modular Space Provider
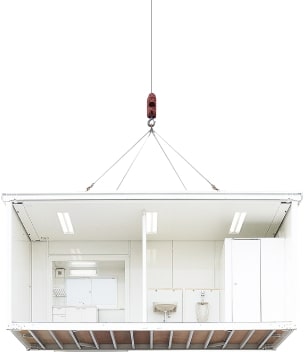
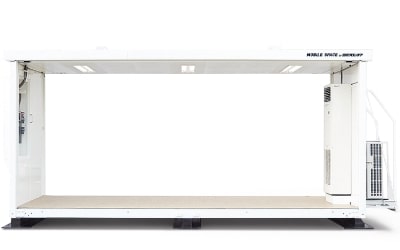
In every space that we create, we strive to make communities — and in turn, the world — a better place for all.
Combining the best of innovation with environmentally sound philosophies, we are proud to be a partner in solving your modular space needs.
Our prefabricated modular products are versatile, suitable for many different uses across a variety of industries.
Case Studies
Our case studies feature modular space solutions for various industries, such as retail, education, events and construction.
Explore how others have created their own modular spaces with Mobile Space by Sankyo Frontier.
Temporary Accommodation for Emergency Relief Efforts
Hair Salon
Company Office
Modern Pharmacy
Clubhouse Cafe
Coin Laundry
The Modular Advantage
Tough space problems call for tough solutions. Our steel, rigid-framed products are strong enough to withstand nature’s harsh elements — even earthquakes. The steel girders are also rust-proofed through hot-dip zinc galvanizing.
Tough Protection All Around
To create a comfortable interior without pillars, each unit is defined by a tough box frame that does not require braces or strong walls. Pillarless spaces of up to 9m wide can be created; the largest in Japan’s modular construction industry. In addition, we are constantly increasing safety standards, running tests in the event of natural calamities such as storms and earthquakes.
Fire-proofed for Safety
Fire-resistant phenolic foam is incorporated into the wall and roof insulation. Non-combustible ceiling sheets are installed, and corrosion-resistant cement boards are used for the flooring to improve walking comfort and heat resistance.
Building Certification Compliant (in Japan)
Our modular units comply with building regulations for temporary buildings, and we use a life-sized testing chamber to perform strict checks on the structure to determine it performs as intended. Be it for events or sales offices, or any type of space, we provide buildings that comply with each country’s regulations.
No Proof Wall Required
Because each unit is a structure that supports all loads with just four pillars, there is no need for obstructive sections and load-bearing walls that restrict the layout. The result is an open space with an easy-to-use layout.
The Right Balance of Speed and Safety
The steel foundation* can be easily adjusted by bolting the steel plate and H type steel. Durability and design are improved by plating and phosphate treatment. If required, our team can assist you in acquiring a building permit (only applicable in Japan).
* Because materials are made-to-order, delivery may take time.
Earthquake Resistant
Our products comply with Shizuoka’s earthquake resistance standards, which are the strictest in Japan.
Improved Thermal Insulation
Incorporated in the roof is the same insulation that has been used to fortify the exterior walls of the main building. By reducing the possibility of transferring cold air and heat, we keep the room temperature comfortable throughout summer and winter.
Our modular solutions are dynamic, customizable, foldable and therefore can be flat-packed for easy transportation. They can be easily remodelled, relocated and removed as your needs change. This flexibility also enables us to export products made in Japan more easily.
As Flexible As Your Imagination
A simple, sophisticated design that can be used both for temporary and permanent installation: the Box Connection. Buildings are simply installed by following the instructions as stated in the manual. The design of the links between the frame and panels have been thoroughly thought through, and the unit does not use temporary joints.
Any Size, Every Need
Each unit can be connected vertically and horizontally, accommodating to various space sizes and needs.
Concealed Electrical Fixtures for a Clean, Modern Interior
In every unit’s electrical system, an EPS panel is adopted, concealing the wiring. The single phase, 3-wire system and 200V electrical lamp used now correspond to normal standards.
Customisable Materials
Whether it is a rental or sale unit, customisation of the design is possible – with a wide array of options such as FIX glass, louver panels, wave panels, and more. Both the interior and exterior can be customised as well.
A Wide Range of Options
A flexible layout, with fast and safe construction, our modular structures can be used for all spaces such as construction site offices, home sales offices, event facilities and more.
(Swipe right/left to view information)
(Modular) Unit House | Prefab | Conventional Construction Method | |
---|---|---|---|
Construction Speed | Quite fast | Normal | Slower |
Extension and Renovation | Easy | Pre-planning required | Requires time |
Relocation | Easy | Possible | Challenging |
Quality | Consistent quality | Normal | * Depends on the skill of craftsmen |
Design Freedom | Selected | High | High |
Recyclability | High | Normal | Low |
Earthquake Resistance | High | High | * Depends on the skill of craftsmen |
* Because materials are made-to-order, delivery may take time.
We carry out all assembly processes of the modular products in our factories, so our modular buildings require little on-site construction time, which means speedy assembly, whatever the weather.
Construction Time Comparison
Modular Building vs Conventional Building
Modular Building
Required construction time: 25 days


Conventional Building
Required construction time: 55 days
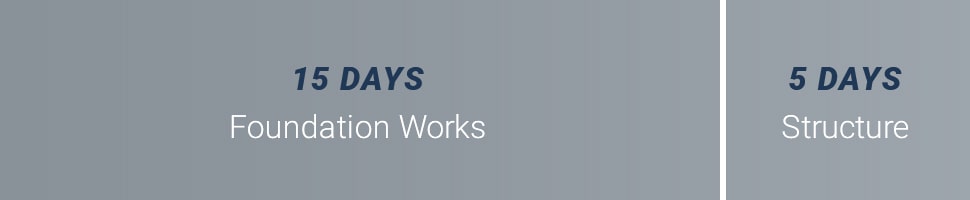

* Estimate based on a 2-storey building with 76m2 of floor space.
** Based on use of stick foundation for the method of unit house construction.
*** Construction time may differ according to interior/exterior specifications, site circumstances, etc.
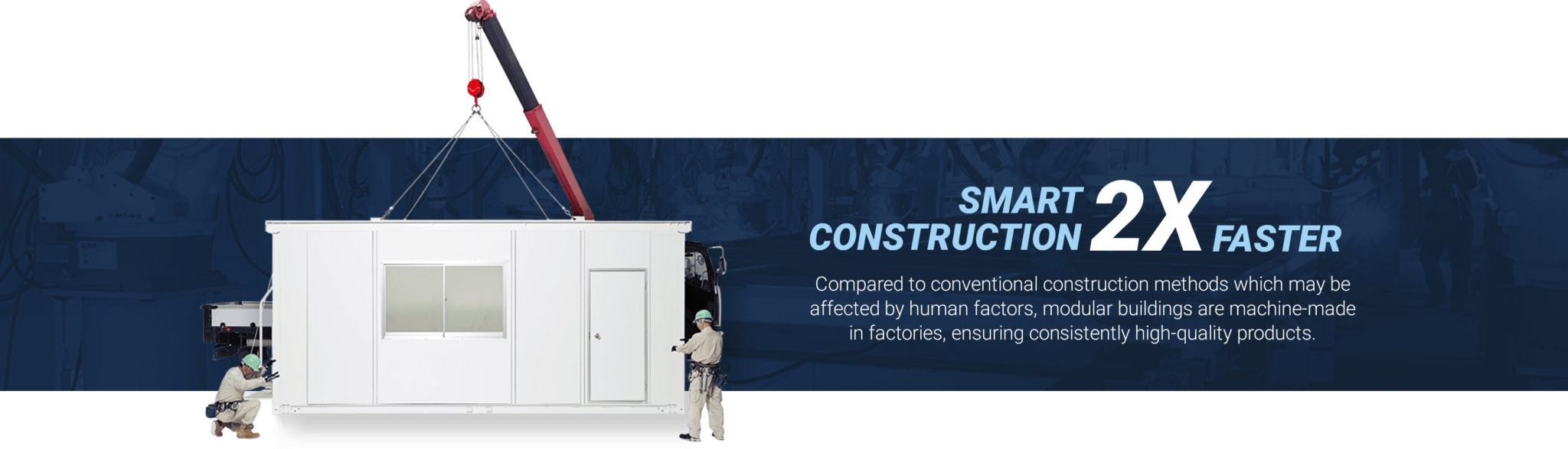
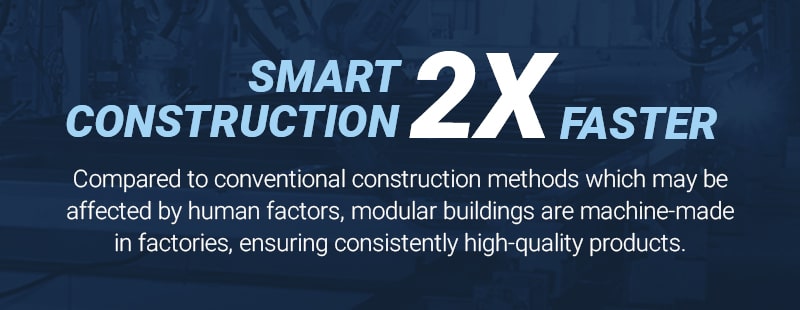
Our Flatpack Transport System
To ensure fast construction, we designed our modular units to be folded into a flat, easily transported state. This allows up to six units to be transported at once, a time and cost-saving feature that can reduce CO2 emissions by 1/6.
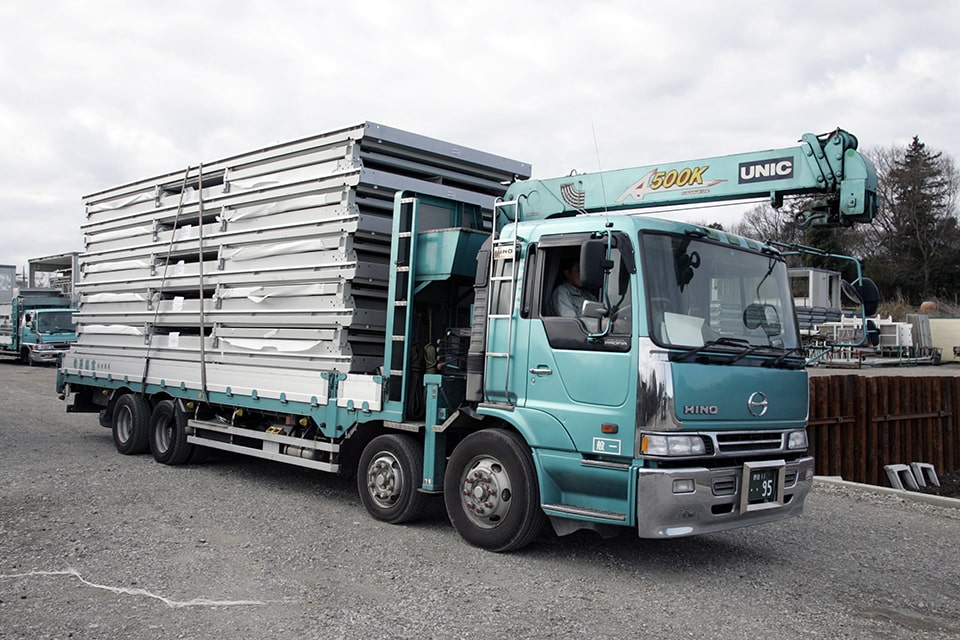
Step 1
Transport and Shipping
Our modular units are manufactured, inspected, and shipped from our factories in Japan.
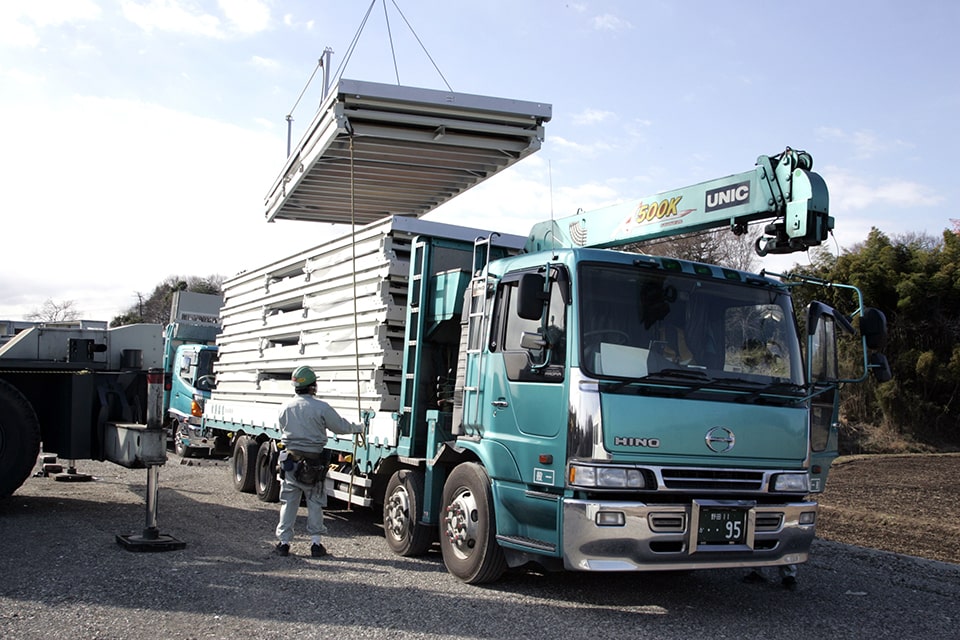
Step 2
Construction Begins
When the units arrive at the construction site, only a crane and a small team is needed to unpack and assemble the units. The crew secures the crane to a unit, which is lifted to its intended location.
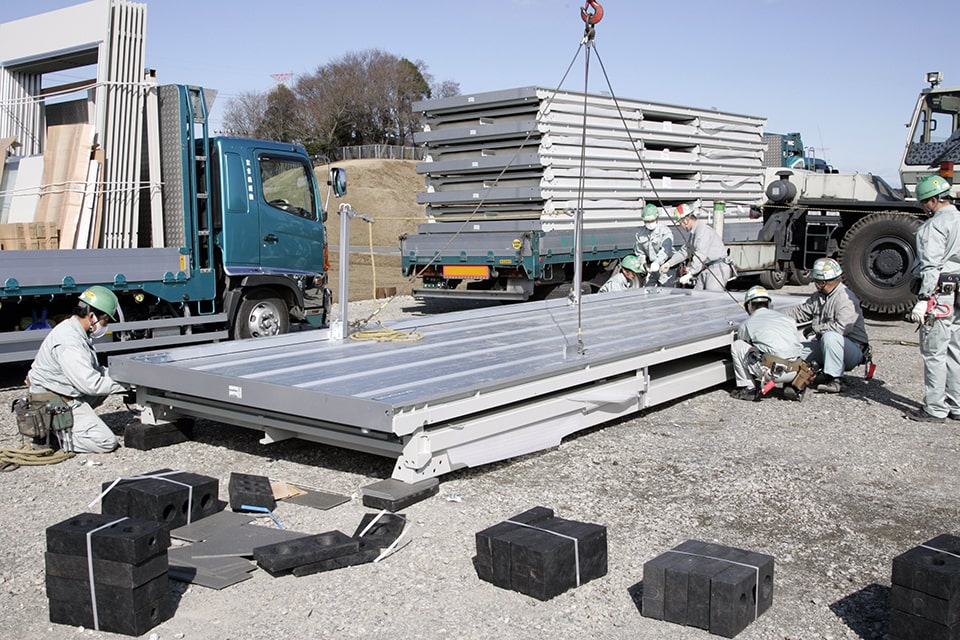
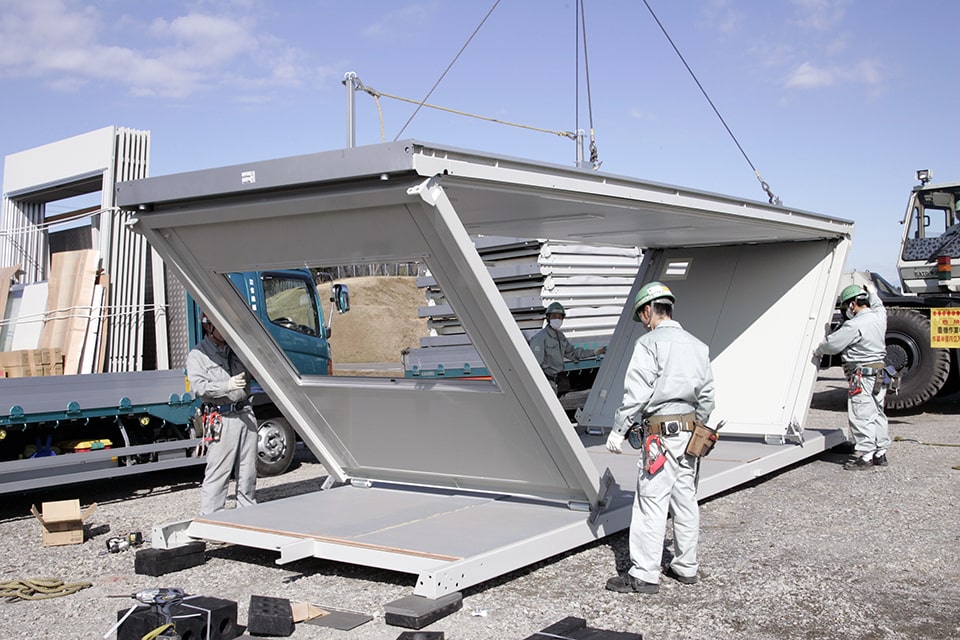
Step 3
Once the unit is in place, the crane lifts the roof, unfolding the unit.
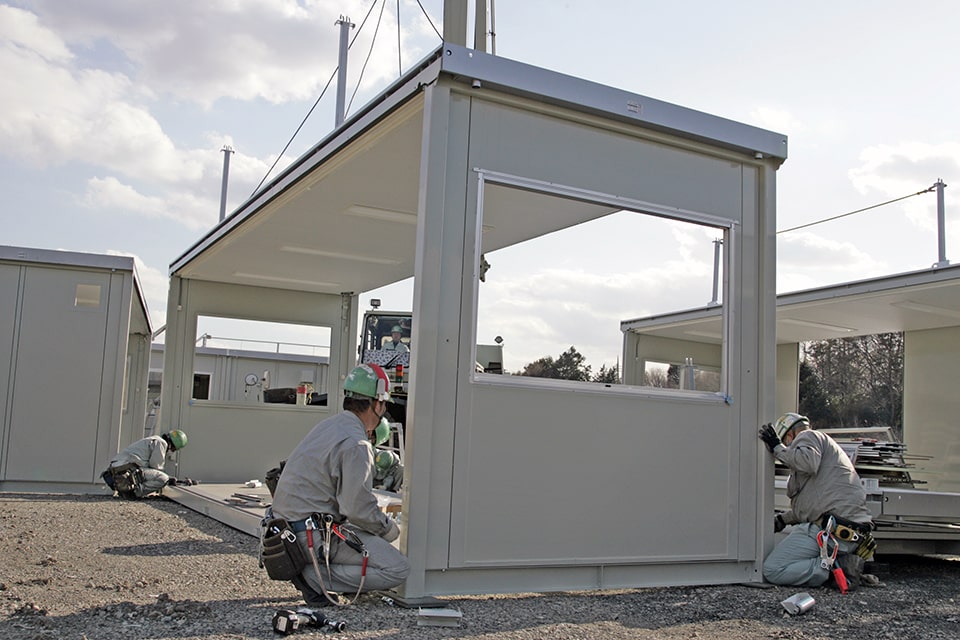
Step 4
Once safety is assured, the crew then bolts down the pillar, roof and floors.
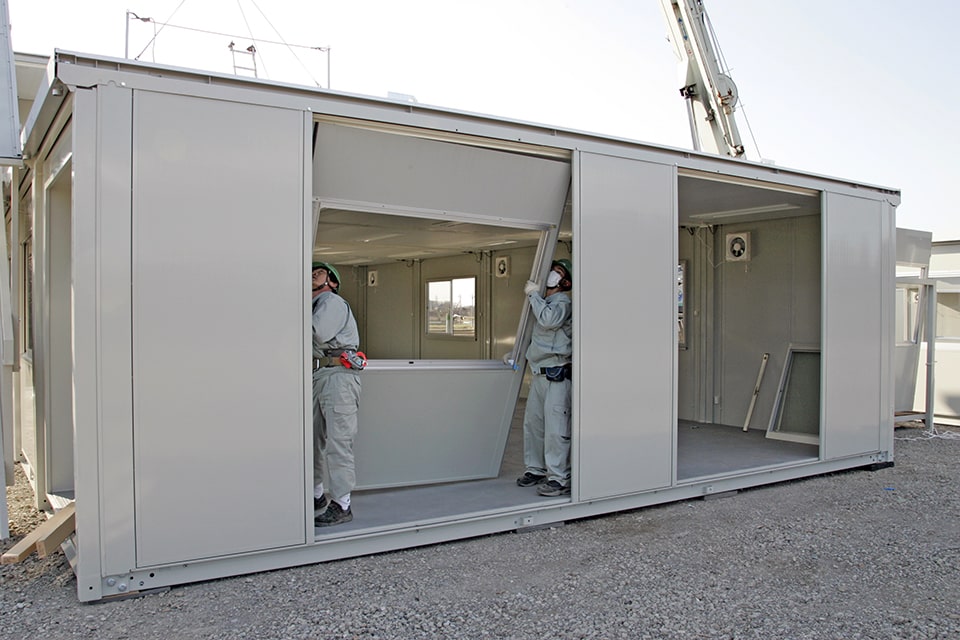
Step 5
Customisation of Unit
With the frame complete, systemised wall panels, glass doors, stairs and other features are installed to customise the building’s appearance.
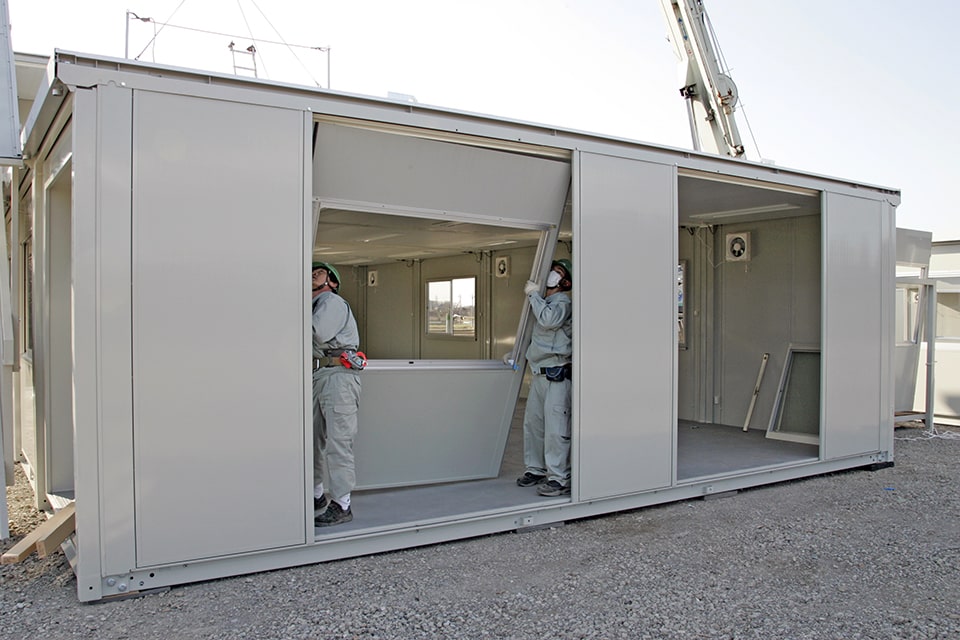
Step 6
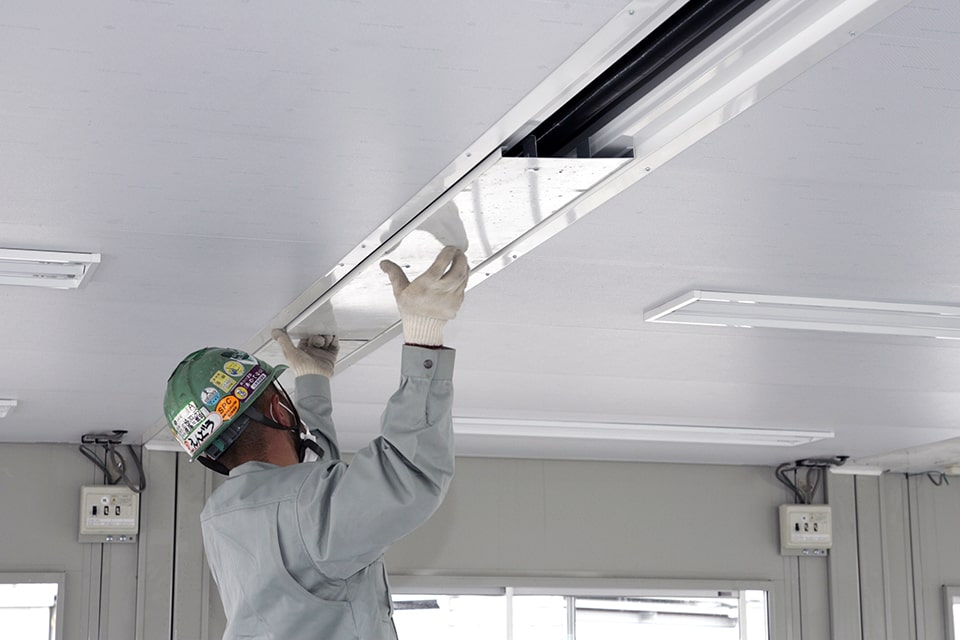
Step 7
Installation of Electrical Fixtures
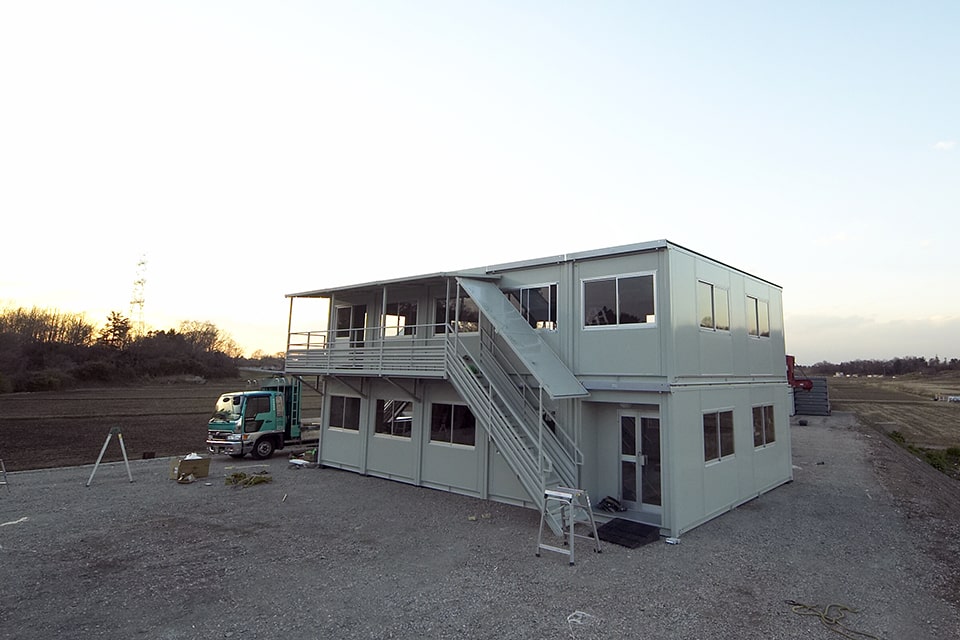
Step 8
Safety is paramount, from production to installation. Products are well fabricated and installed to ensure safe usage for both our employees and customers.
Safety by Construction Procedure
When constructing a multi-storeyed building, setting up stairs instead of a stepladder significantly improves safety at work.
Safety Indoors
Since the installation and maintenance of air conditioning units and electrical wiring can be done onsite, within each unit, no stepladder or working at height is required. In addition, installation of facilities can be done concurrently with the construction of the building, cutting down on time considerably.
Safety during Electrical Wiring Work
By installing electrical wiring in the factory in advance, wiring work is greatly simplified. Onsite, electrical work can be completed simply with a connector, so the construction process is safe.
Safety during High Altitude Work
We take safety measures seriously. By tying the main rope and connecting it to a safety belt, the safety of our workers – even at high altitudes – is assured.
Safety during Crane Operation
By lifting the roof and adopting a “butterfly construction method”, the pillars can automatically be erected. This way, no manual power is needed, resulting in a smaller team. So it’s not just efficient – it’s safe too.
Safety during Maintenance
During maintenance, there is no need to use the stepladder to access the roof from the second or third floor – workers can head to the roof via stairs, which are more stable and safe.
Purchase vs Rental
Depending on your needs, we have products available for rent or purchase.
Length of Usage
Ideal for temporary buildings for industrial or commercial purposes (between 1 day to 2 years)
Cost
- Affordable initial investment
- Monthly rental fees are more cost-effective for short-term use (under 2 years)
- Property taxes not required
Customisation Options
Good variety of options available for customising your modular space
Length of Usage
Ideal for long-term establishments like schools, hospitals or other institutions
Cost
- Larger initial investment
- Cost-effective for long-term use (over 2 years)
- Building maintenance and repair costs required
- Local property taxes may apply
Customisation Options
Greater variety of options available for customising your modular space
Our Solutions
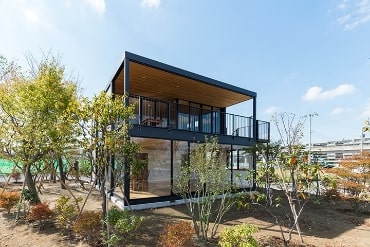
MS1
The MS1 is the premium selection of modular units that is strong, energy-saving and highly versatile. It is also made 25% more rigid and 16% stronger than comparable products in the market.
Learn more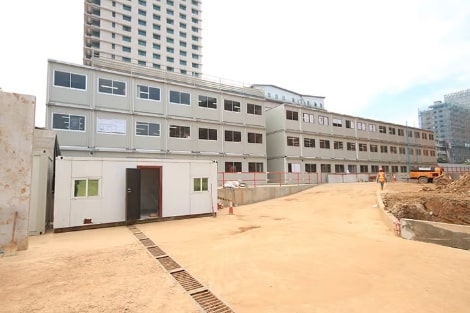
CT-J
The CT-J is a basic series of modular units with a unique folding structure that is strong yet economical. It can be used for portable offices, temporary site offices, temporary shops.
Learn more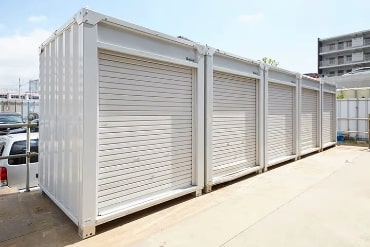
Gorilla
The Gorilla is a portable storage unit to keep valuable cargo such as furniture, machines, or other essential goods protected from inclement weather.
Frequently Asked Questions
How much does a modular building cost?
The cost depends on your requirements for your unique modular space. We have different modular solutions available for purchase and rent, and the prices vary depending on your need. Fill in the enquiry form here, and our team will be in touch to conduct an in-depth personal consultation.
Are modular solutions expensive?
They don’t have to be. Depending on your needs, selecting the right modular products for rental or purchase is a low-risk, high-value investment.
For modular solutions on rental, the initial investment is lower than buying. However, it only becomes non-cost effective if the duration of usage is undecided and gets stretched on a month-to-month basis. When renting a modular space, it’s essential to have a clear idea of the exact usage purpose and duration to compare the cost and affordability of purchasing the modular space.
For modular solutions that are purchased, it becomes more cost-effective for long-term usage. Because of its durability, strength and higher customisability , it can serve as a long-term solution for brands that foresee the usage duration to be anywhere from 2 to 20 years.
Sankyo Frontier’s wide range of modular products allows you to find the best solutions to your needs. From the CT-J basic series to the Gorilla series, our modular spaces give you great flexibility and choice for industrial, residential or commercial purposes.
Fill in the enquiry form here, and a member of our team will be in touch to conduct an in-depth consultation with you.
What is the difference between renting and buying a modular building?
Requirements | Rental | Purchase |
---|---|---|
Length of Usage | Ideal for temporary buildings for industrial or commercial purposes (between 1 day to 2 years) rental or purchase.
Rental modular products are suitable for use for up to 2 years. | Ideal for long-term establishments like schools, hospitals or other institutions |
Cost |
* Please note that costs may vary depending on the project’s requirements. |
|
How long do modular buildings last?
We have segmented our modular products to fit two modes of use — rental or purchase.
In general, modular buildings are extremely durable and fit for long-term use for up to 20 years. Read our case studies to find out how versatile our products can fit into both the commercial, industrial and residential needs of users across the globe.
What is the floor load capacity of the modular products?
Most of our products, such as the MS1 and CT-J units, can withstand up to 295kg/m2. If you have a specific project you’re exploring for our modular solutions, drop us an enquiry and our team will be in touch to conduct an in-depth personal consultation.
What materials are used to produce Sankyo Frontier’s modular units?
Each of our modular units is constructed with lightweight steel, coloured steel plate walls, and plywood. All units are also insulated with styrene foam and moisture-proof sheets to ensure the buildings are weather-proof. All units are designed to be easily transported, assembled and dismantled with reusable materials. Only a simple crane and a small team are needed to assemble the prefabricated modular units on site.
Our MS-1 series, for example, is also 25% more rigid and 16% stronger than conventional modular products that you find on the market. Learn all about the MS-1 series here.
What is the difference between our modular units versus commercial shipping containers?
Our modular units are superior to shipping containers in three key aspects: Safety, Customisation, Convenience. Our modular units are safe and built to withstand harsh elements and comply with Japanese building regulations, which have some of the strictest building codes in the world. No extensive modifications need to be carried out to ensure the safety of the occupants within the unit. Furthermore, our units also have electrical wiring and lamps pre-installed, which reduces time spent to custom-fix wiring and fixtures compared to shipping containers that come bare-bodied.
How can I customise my modular space?
To fit your project’s brand guidelines and needs, we offer options to modify building features like staircases, wall panels, facilities, and modular building exteriors and interiors.
For more details on making a modular space uniquely yours, fill in our enquiry form for a personal consultation with our team.
Check out our past case studies of modular solutions that we’ve provided our satisfied clients over the years.
Do the modular products come in fixed dimensions?
Yes, our modular products come in fixed dimensions, but you can stack them horizontally or connect them vertically for bigger space needs. If you have a specific land space dimension limitation, chat with our friendly team to get a detailed personal consultation.
What is the extent of customisation I can make?
The extent of customisations will depend on whether the modular space is a rental or purchased. Generally, purchased modular spaces can have a greater degree of customisation, whereas rented modular spaces have more limited customisation.
For more details on customising a modular space that is uniquely yours, fill in our enquiry form for a personal consultation with our team.
You can also check out our past case studies of modular solutions that we’ve provided our satisfied clients over the years.
How long does it take to build a modular building?
Our modular units are designed for easy assembly, and we can build about eight units in a day. Furthermore, as almost all assembly processes occur in our factories, our modular buildings require little on-site construction time. It is also safer and reduces unnecessary potential on-site injuries. For more details, please write to us via the enquiry form.
What are the processes involved in building a modular building?
Multiple layers of decision-making, logistical requirements and planning are needed to erect the desired modular space.
A robust modular building design involves precise design specifications, safety and regulation clearances, permissions from the authorities, site preparation, transportation of the unit modules and installation. Sankyo Frontier designs modular solutions so that most of the heavy lifting (preassembly) occurs in our factories. They are then transported, assembled and installed safely using a simple crane alongside the support of a small team for supervision.
Learn about the 101s on modular buildings here.